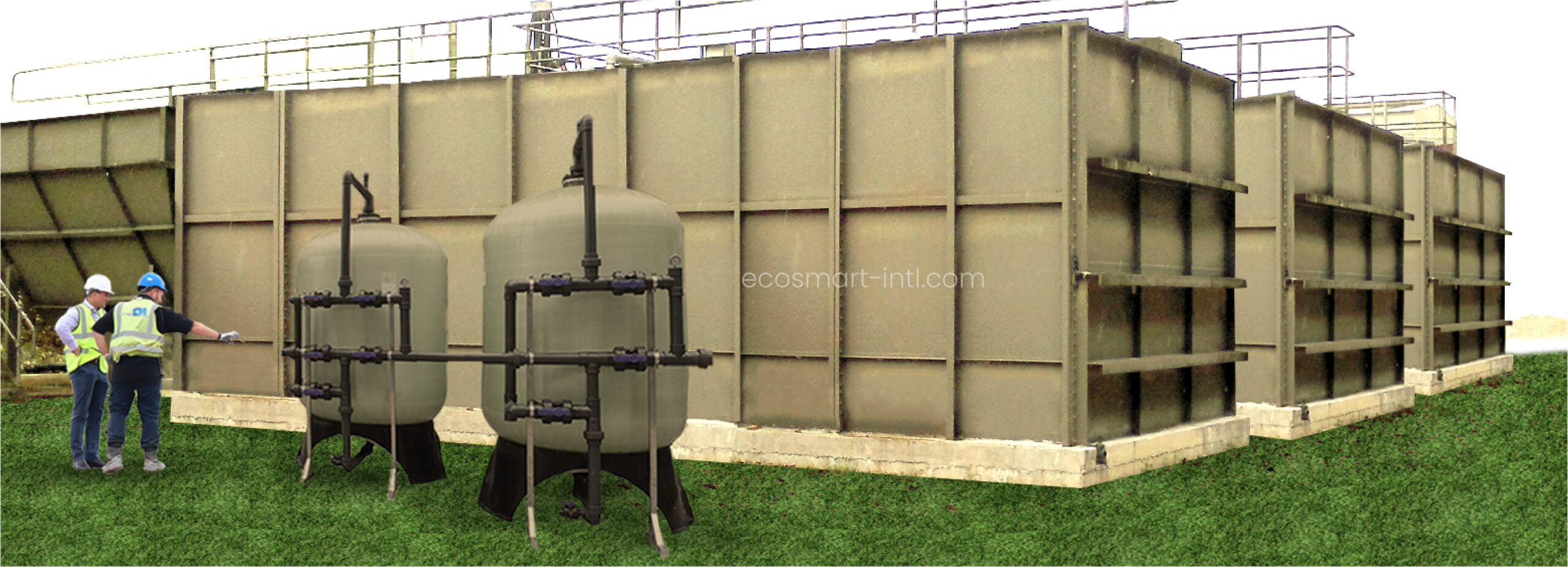

Biological Reactor Treatment Plants
The MBBR Technology is a robust and inexpensive Biological Wastewater Treatment than conventional Biological Treatment. As a result of more research work, an engineered plastic media is used to promote fixed biomass. This makes for an efficient and easy-to-operate Wastewater Treatment that does not require any recirculation of the mixed liquor suspended solids (MLSS). The MBBR Technology can be used for both the treatments of carbonaceous and nitrogenous pollution and also in both municipal environments (activated sludge, lagoons, etc…) or in an industrial setting (landfill leachate, food and beverage industry etc…). Fresh water taken from nature is pure. It is utilized and recycled carefully within the processes and when returned to nature, the water has to meet the highest standards for sustainability. These targets can be achieved by Eco Smart Biological Treatment Solutions.
MBBR PROCESS
The MBBR Process is the development of the biomass that moves in the biological reactor via agitation generated by Aeration Systems in aerobic reactors or by Mechanical Systems in anoxic or anaerobic reactors. Even when the capacity reaches 70%, the supports are made from plastic with a density close to 1 g/cm3 allowing them move easily in the reactor. The Moving Bed Processes in Wastewater Treatment achieving significant reductions in the biological reactor volume. Originally the Fixed Bed Systems were used. However it was discovered that this type of process show a series of operational problems such as the blocking of the bed because of the excessive growth of the biomass and this makes periodical cleaning obligatory. These drawbacks have initiated the need for the creation of easy biofilm processes that remove them and that ease their operation; these are the moving bed processes.
This type of process can be useful to both treatment plants for the biodegradation of organic material as well as for installations with nutrient elimination, in industrial and urban wastewaters.
Advantages :
- Constant for water quality and quantity fluctuations
- High efficient treatment
- Requirement of low space
- Simple operation
- Highly reliable excess sludge
- Expandable and compact
- Biological effective system
- Speedy start-up and restart
- Low volume sludge
- Low power consumption
- Stable and durable process
- Easily transported plant to site
- Pre-fabricated and pre-engineered
Applications :
- Schools and universities
- Power plants and manufacturing facilities
- Residential, hotels and resorts
- Military bases and construction sites
- Food Processing Plants etc.
Wastewater treatment systems using bio-films that grow attached to a support media are an alternative to the widely used suspended growth activated sludge process. Conceptually, the process Biodegradable Effluent Treatment is extremely simple. A small amount of microorganisms converts a large mass of polluted water into clean water. This process also produces a co-product: A vastly reduced, compact solid biomass (the excess microorganisms produced by growth and multiplication of the original population of microorganisms).
The micro-organism employed for the treatment of effluent can be anaerobic or aerobic. The anaerobic micro-organisms are those live in the absence of oxygen and the oxygen is a poison to them. The aerobic micro-organism is those living with oxygen and they need oxygen for survival. The anaerobic treatment requires higher tank volumes, but requires very less operating cost. The aerobic treatment is highly machine-oriented and requires less tank volume and high operating cost.
In Eco Smart FBBR (Fixed Bed Bio Reactor) technology, we provide a packing media (structured matrix of polypropelyne media) for enhanced growth of microorganisms in inert materials in the aeration tank, so that the surface area increases and which allows more bacteria to grow and enhance the process.
Details of each Treatment Systems:
Screen Chamber:
The function of the bar screen is to prevent entry of solid particles/ articles above a certain size; such as plastic cups, paper dishes, polythene bags and cut pieces from slaughter area into the STP. (If these items are allowed to enter the STP, they clog and damage the STP pumps, and cause stoppage of the plant.)
The screen chamber must have sufficient cross-sectional opening area to allow passage of sewage at peak flow rate (2.5 to 3 times the average hourly flow rate) at a velocity of 0.8 to 1.0 m/s. The screen must extend from the floor of the chamber to a minimum of 0.3 m above the maximum design level of sewage in the chamber under peak flow conditions. Bar screen racks are typically fabricated out of 25 mm x 6 mm bars either of epoxy-coated mild steel or stainless steel. A specified opening gap is kept between the bars. The screen frame is fixed in the bar screen chamber at an angle of 60º to the horizontal, leaning away from the incoming side. The grease and grit trap is placed at the discharge point of the canteen/ kitchen area itself to arrest solid and fatty matter at source. The wastewater output from this unit is taken to the equalization tank.
Oil and Grease Trap
An Oil and grease/grit trap is generally not an essential unit in a typical residential complex. The length of trap should be approximately 2 times its depth residence time in the trap is optimally 5-20 minutes at peak flow. Surface area of the trap in m2 should be approximately 1.5 to 2 times the depth of trap in metres.
The tank should have waterproof plastering inside and out. The end of the incoming pipe is kept below the water level, so that the incoming water does not disturb (and break up) the upper floating layer of grease.
The trapped material (both floating film of grease/ fat and the grit settled at bottom) must be collected frequently; otherwise the trap will fail to serve its fundamental purpose. Therefore the trap must be engineered to facilitate frequent removal of these two layers. For example, the covers must be made of lightweight materials for easy lifting. Large traps may be provided with vent pipes to release gases.
Equalization :
The equalization tank is the first collection tank in an ETP. Its main function is to act as buffer: To collect the incoming raw Effluent that comes at widely fluctuating rates, and pass it on to the rest of the ETP at a steady (average) flow rate. During the peak hours, effluent comes at a high rate. The equalization tank stores this effluent, and lets it out during the non-peak time when there is no/little incoming sewage. Thanks to the constant outflow rate, it is easier to design the rest of the units of the ETP.
Since the diurnal variation in the quality of the effluent is not significant, the equalization tank is used only for buffering the daily fluctuations in the sewage flow quantity. The equalization tank must be of sufficient capacity to hold the peak time inflow volumes. Peak times and volumes are site-specific and variable.
The incoming effluent line is usually gravity-fed, and is likely to be at considerable depth below the ground level. The tank may be of any shape, provided it permits placement of air diffusers for full floor coverage and uniform mixing over the entire floor area. The diffusers should be retrievable: Individual diffusers (or sets of diffusers) may be lifted out and cleaned for routine maintenance. This will reduce frequency of shut down of the Equalization tank for manual cleaning purposes.
Fixed Bed Bio Reactor :
Eco Smart FBBR gives an enhancement to the microbiological growth by providing more desirable growth surfaces by adding increased surface area in the bio-media. The biological growth is protected by carefully designed packing FBBR media with high internal surface area.
When communities of microorganisms grow on these specially designed bio-media, the micro-organism is more resistant to process disturbances compared to other types of biological treatment processes. With this technology it is possible to handle extremely high loading conditions without any problems of clogging, and treat industrial and municipal wastewater on a relatively small treatment tanks. Thus, this technology can be considerably more robust especially when compared to conventional technologies like activated sludge process.
The wastewater is led to the reactor where biological growth within the internal structures of the biomedia enhances the digestion of pollutants. These pollutants that need to be removed in order to treat the wastewater are food for the micro-organisms.
An aeration grid (coarse bubble diffusers) located at the bottom of the reactor supplies oxygen to the bio-media along with the mixing energy required to keep the media suspended and completely mix within the reactor. Treated water flows from reactor through a grid or a sieve, which retains the biomedia in the reactor. Specially engineered FBBR bio-media shall be with following details:
Bio-media Type : Corrugated arranged in blocks
Material of construction : Polypropylene/ Polyethelene/PVC
Strainer : Polypropylene/PVC/FRP
Specific Gravity : Slightly higher than water
Clarifier :
The purpose and function of the secondary clarifier is threefold: Allow settling of biomass solids in the Mixed Liquor (biomass slurry) coming out of the aeration tank, to the bottom of the clarifier To thicken the settled biomass, in order to produce a thick underflow To produce clear supernatant water, in the overflow from the clarifier The clarifier tank is only a passive device: All the above actions occur due to gravity. The thick biomass is re-circulated back to the aeration tank.
The clarifier tanks can be classified in two groups: mechanized and un-mechanized. In an un-mechanized clarifier, the bottom of the tank is shaped like a funnel, with a steep slope. The sludge slowly settles towards bottom, and slides down the slope to collect at the lowest point of the funnel-shaped bottom. In a mechanical clarifier, the bottom of the tank has only a gentle slope toward the center. The sludge settles uniformly across the floor of the tank. A set of slowly rotating rubber blades sweep the sludge into a hopper at the center of the tank
Pressure Sand Filter
The pressure sand filter (PSF) is used as a tertiary treatment unit to trap the trace amounts of solids which escape the clarifier, and can typically handle up to 50 mg/l of solids in an economical manner.
This unit is essentially a pressure vessel that is filled with graded media (sand and gravel). The water filtered with PSF is passed on to the next stage in the ETP chain: the Activated Carbon Filter. A good average design filtration rate is 12 m3/ m2/hr of filter cross-sectional area, and most filters used in STP applications are designed on this basis.
The Filter vessel is designed as a pressure vessel (it consists of a straight cylindrical shell, with convex dish-shaped ends welded to the top and bottom). A typical vessel is designed to withstand a pressure of 5 kg/cm2. In large filters, a manhole of > 0.6 m dia is provided at the top. A hand-hole of > 200 mm dia is provided at the bottom of the cylinder to facilitate removal of media from the vessel at the time of servicing. A set of pipes, valves, bypass line, backwash waste line etc. are also provided to facilitate operations such as filtration, bypass (during servicing), backwash etc.
Activated Carbon Filter
An activated carbon filter, like the Pressure Sand Filter, is a tertiary treatment unit. It receives the water that is already filtered by the Pressure Sand Filter and improves multiple quality parameters of the water: BOD, COD, clarity (turbidity), colour and odour.
This filter uses the adsorption action of activated carbon. Activated carbon is typically manufactured from coconut shell or charcoal, the “activation” process creating a highly porous material with a very large surface area. Organic pollutant molecules are physically adsorbed and held fast within the catacomb-like porous structure of the activated carbon. Granular activated carbon is typically used for this purpose. The water filtered by the Pressure Sand Filter enters the Activated Carbon Filter. Unlike in the case of the sand filter, trapped molecules in the carbon cannot be backwashed and got rid of. Hence, activated carbon in the filter has a finite capacity to adsorb and hold the pollutants, after which the carbon is said to be exhausted. The exhausted material is removed from the filter and disposed off: Fresh activated carbon is charged in the filter.
Disinfection System :
The treated water is disinfected to destroy and render harmless disease-causing organisms, such as bacteria, viruses, etc. The most common methods of disinfection include Chlorination, Ozonation and UV radiation. We are using Chlorination as a Disinfection System in our FBBR.
In most STPs, the common form of Chlorine used is Sodium Hypochlorite (Hypo) available commercially at 10-12 % strength, being safe, easy to handle and having a reasonable shelf life.
Efficiency of disinfection is dependent both on the residual concentration of the chemical used, as well as the contact time, a factor measured as R x T. Generally, a contact time of 20-30 minutes is recommended to achieve over 99 % germicidal efficiencies.
The Chlorine disinfection system consists of a Hypo-holding tank (its size depends on the flow rate of the ETP) and an electronically metered dosing pump. Hypo solution of desired concentration is prepared in the tank. The dosing rate is set in the metering pump as per the desired Chlorine dose rate, typically 3-5 PPM. Hypo solution is dosed at the outlet of the ACF, online, so that adequate mixing of Hypo with the treated water is achieved.
Sludge Handling :
Biological treatment of wastewater perforce produces excess biological solids due to the growth and multiplication of bacteria and other microorganisms in the system. The excess biomass thus produced needs to be bled out of the system, and disposed off efficiently.
Sludge is also generated from the primary settling tank. The sludge is in the form of a thick slurry. It is taken into a Bio-gas plant or a bio-digester tank. The digested sludge is evacuated periodically and used as bio-fertilizer.
Filter Press :
The filter press is designed for the dewatering of the liquid sludge generated by wastewater treatment plants In a filter press sludge dewatering is achieved to reduce significantly the percentage of moisture in the dewatered sludge, to a large extent by reducing the amount of waste to be managed
Filter presses are highly efficient for removing water from sludge. Filter presses operate on feed pressure and can be used for high volume separation of solids from slurries, utilizing recessed or membrane plates. When the wastewater passes through the filter plates the discharge system and the filter medium retain the solid particulates. The wastewater slurry is continually fed into the system until all the water is squeezed out. The remaining solids form a dry cake and are collected in a basin prior to disposal.
Eco Smart Submerged Aerobic Fixed Film Reactor is a cost-effective method of waste water treatment and sewage sanitation. SAFF technology utilizes an aerobic fixed film process that is a combination submerged attached growth and activated sludge processes. Essentially SAFF system is a hybrid reactor where attached growth and suspended growth activity takes place simultaneously. Eco Smart Submerged Aerated Filter plant has no moving parts within its main process zones, any serviceable items will be positioned to access easily without disrupting the ongoing sewage treatment.
The four stages of SAFF process :
- Primary Settlement
In primary settlement process the larger solids settle into the bottom of the primary tank and are removed periodically as sludge, and the materials floating upwards is removed by a screening method.
- Secondary Settlement
In secondary treatment process Aeration is done intermittently using diffusers which helps in reducing BOD/COD of the sewage. Aeration of wastewater with flocculating biological growth, followed by separation of treated wastewater from this growth. Fluidized suspended media circulates within a basin, and the bio-media is engineered in a wheel shape & is buoyant, allowing water flow to circulate the media throughout the vessel. It has high bio-surface area and the bio media design allows aggressive sloughing action thus maintaining a productive layer of biological growth.
- Final Settlement / Clarification
Where remaining solids (Humus) are settled out of the biological treated effluent.
- Optional Post Filtration / Sterilization
Optionally further polishes treated water for specific applications
Advantages of Eco Smart SAFF systems:-
- SAFF supports low sludge generation, low Odour and low visual impact
- Make bio system extremely compact
- Clog free operation, High bio surface area
- Easily retained media with long life
- No interruption to process
- No sludge return system needed
- Effective under extremely high BOD loading
- Less sensitivity to shock loading
- High effluent quality
- Small footprint, simplicity of design, installation & operation
- Design flexibility, easy affordable up-gradation
- Maintenance requirements are simple.
The Latest Technology in the Wastewater Treatment is the Membrane Bio Reactor. Membrane Bio Reactor has many advantages such as:
- High quality of treated water
- Small space for installation
- Easier process compared to conventional Activated Sludge Process
Membrane Separation Technology called as Membrane Bio Reactor which produces high quality water with maximum possible bacterial reduction without adding chemicals. The Membrane Bio Reactor (MBR) is the latest technologies in Biological Treatment. The characteristic of the MBR Process is the use of revolutionary submerged ultra filtration membranes in the biological process water tank to produce high quality permeate from
- Domestic sewage
- Primary and secondary waste water
- Cooling tower blow down
The Membrane Bio Reactor is also ideal for supplementing capacity/quality of existing wastewater plants/ retrofitting. The MBR can handle very high sludge concentrations in the ventilation tank because of the size of the aeration tank reduces 4-5 folds. The membrane acts as a fine filter; it does not require any further treatment using Activated Carbon Filters, Sand Filters, etc. which are available in any sizes.
Membrane Bio Reactor Module
- The membrane material is PVDF (Poly Vinylidene Fluoride). PVDF is fluorine polymer, which has high constancy for chemicals and good physical strength.
- The form of membrane is fiber reinforced flat sheet membrane.
- The membrane has small and uniform pore size and the rejection property of this membrane is very good.
- All particles with sizes (>) greaterthan 0.1 micron meter can be removed with membrane effectively.
Advantages
Membrane Bio Reactor | Conventional Activated Sludge |
Less Space | More Space |
Contains no clarified tank | Consist of clarified tank |
Faster, efficient, high stability of sludge, ease of dispose | Less faster |
Superior quality of treated water, reliable system | Less superior |
Less cost is required | Costlier tertiary treatment is requires for matching the performance of MBR. |
MBR acts like a physical barrier by completely removing bacteria up to 46 and it helps in complete retention of biomass in the aeration basin. | MBR acts like a physical barrier by completely removing bacteria up to 46 and it helps in complete retention of biomass in the aeration basin. |
Less chemical and power consumption | More chemical and power consumption |
MBR does not produce disinfection by-products or bad odors. | Produce disinfection by products and odors. |
Minimum treated units, simple to operate, handling hazardous chemicals | Conventional system is more sophisticated with more treating units. |
Energy intake is extremely low (0.30 kwh/m3) and the treated domestic effluent has a 4 to 6 log (99.99%) removal of total coliform. | Energy consumption is high. |